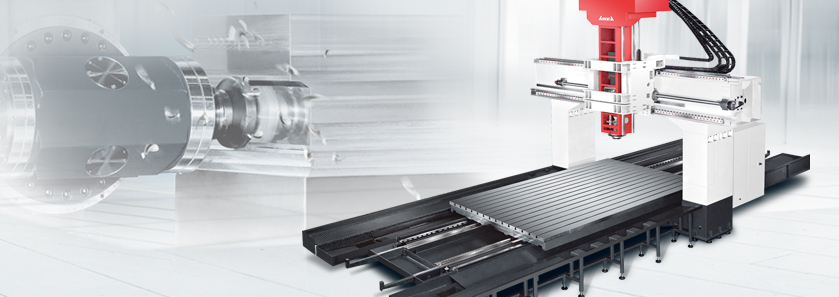
Maximum Strength Construction
Finite Element Method
Employing the Finite Element Analysis ( FEM ) in the design process assures optimal rigidity and helps reducing the machine weight.
Precision hand scraping
The contact surfaces of column, base, cross beam and all sliding members are precision hand scraped to provide maximum assembly precision, structural rigidity, and optimal load distribution.
Roller type linear guide ways
Super rigid roller type linear guide ways on all three axes provide support for heavy-duty cutting and fast, low friction movements.
Precision feedback system
The semi-closed loop system with encoders directly connected to the ball screws ensures high repeatability and positioning accuracy.
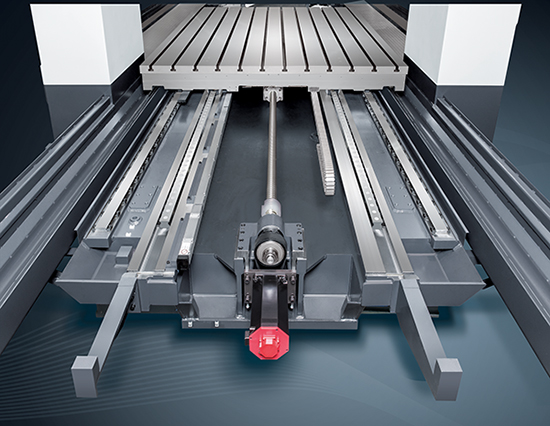
4 guideways on base ( X-axis )
Compound 4 guideways design for maximum structural support and to reduced work table over hang.
Symmetric support center-driven table
Wide span symmetrical center-driven X-axis design with the ball screw placed in the center of the table to provide high precision axial feeding.
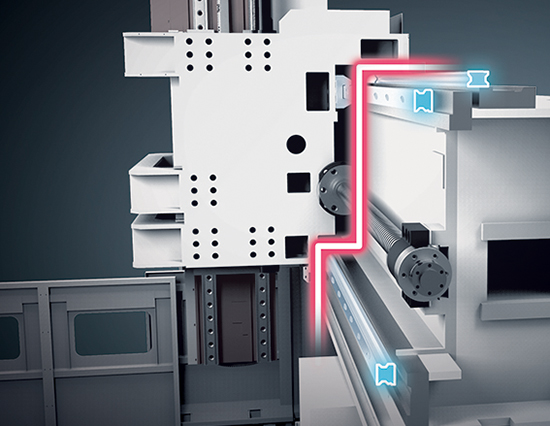
3 guideways Y-axis support
The stepped offset three guideways design of the Y-axis further enhance the rigidity. The new design effectively reduces the distortion due to headstock weight and significantly improves the rigidity for heavy cutting.
Closed loop counterbalance unit
The environmentally friendly closed loop hydraulic counterbalance system enables excellent dynamic movements.